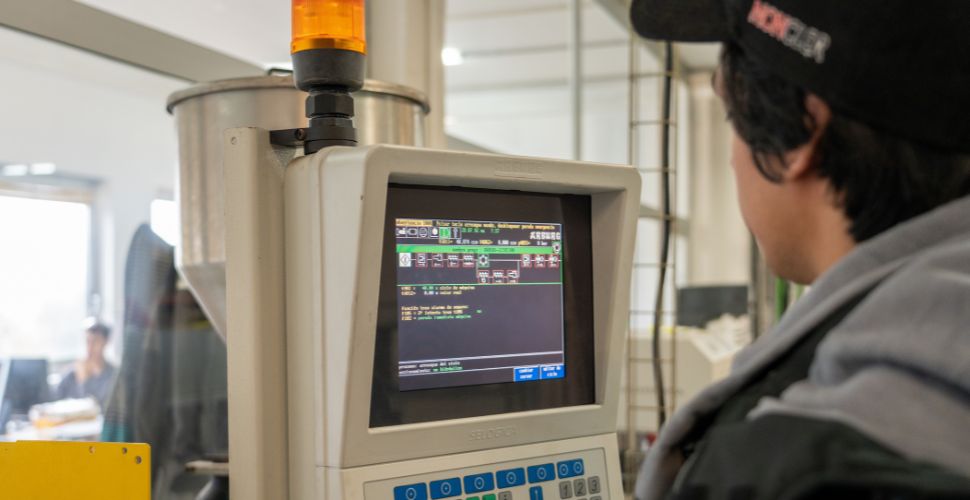
LADICIM Collaborates with CTC on the Smart Specialization of Industrial Processes in Cantabria
The Laboratory of the Division of Materials Science and Engineering at the University of Cantabria is participating in the research line of the FUTCAN project focused on the use of Artificial Intelligence to virtualize industrial prototyping processes.
The Laboratory of the Division of Materials Science and Engineering (LADICIM) at the University of Cantabria is collaborating on the FUTCAN project, an initiative led by the CTC Technological Center aimed at researching and validating new methodologies and technologies to improve efficiency, competitiveness, and sustainability in industrial manufacturing.
FUTCAN is supported by the Directorate-General for Industry, Energy and Mines of the Ministry of Industry, Employment, Innovation and Commerce of the Government of Cantabria. It is co-financed by the European Regional Development Fund through the 2021–2027 FEDER Operational Programme for Cantabria, under the grant line titled “Aid for Research Projects with High Industrial Potential by Technological Excellence Agents for Industrial Competitiveness (TCNIC).”
LADICIM’s collaboration within the “Strategic Positioning for Smart and Sustainable Specialization of Factories of the Future in Cantabria” focuses on the direct use of Artificial Intelligence to virtualize industrial prototyping processes. This is one of the three main research areas of the project, specifically oriented toward the automotive sector. The other two areas involve developing methods to facilitate the adoption of Artificial Intelligence (AI) in manufacturing environments using Machine Learning, and researching new nanomaterial-based coatings that enable early detection and monitoring of degradation in industrial components and structures.
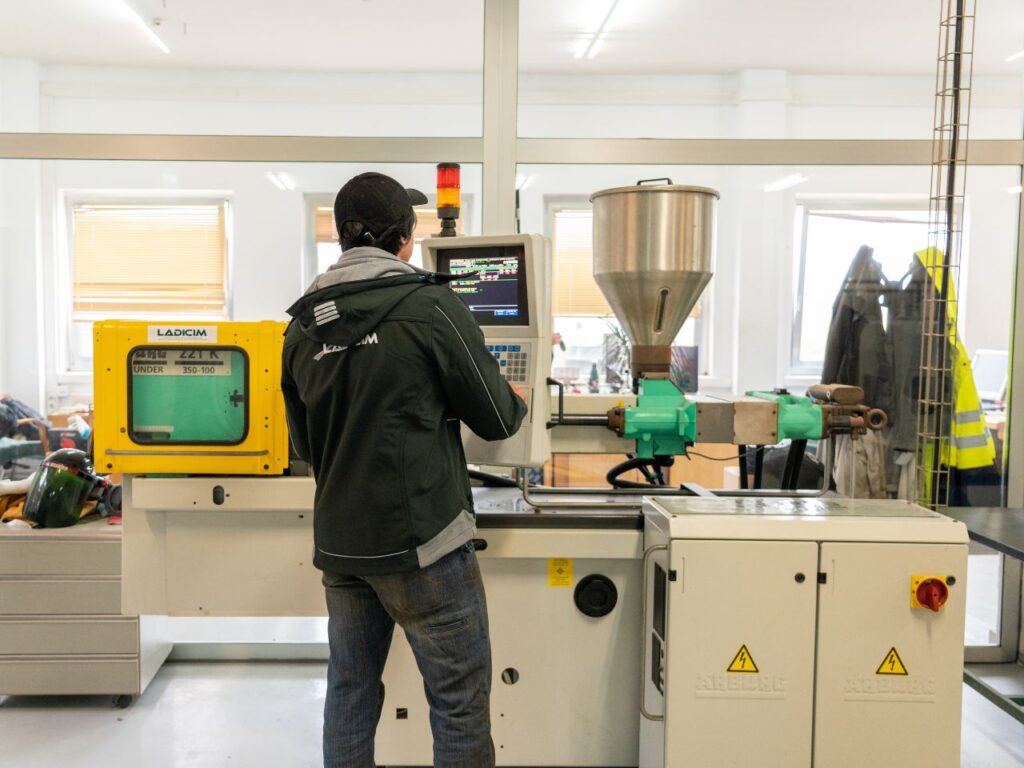
One of the pilot projects within FUTCAN focuses on optimizing the processes of a thermoplastic injection molding machine—a common piece of equipment in the automotive industry used to manufacture a wide variety of components and parts with diverse physical and mechanical properties. The technological advances achieved through this pilot are expected to reduce both production time and material usage by at least 20%, thereby contributing to the efficiency and competitiveness of the automotive sector in Cantabria.
In this context, LADICIM’s connection with the strategic pillars of FUTCAN is direct. The Laboratory holds extensive expertise in polyamide, a thermoplastic widely used in the production of engineering parts and technical components in the automotive, aerospace, and electronics industries due to its excellent mechanical strength and abrasion resistance. LADICIM has also developed several theses and research projects related to this material and injection molding technologies, and it possesses its own industrial-grade injection machine for testing and experimentation. This is complemented by its broad experience in Artificial Intelligence and Machine Learning. For the CTC Technological Center, this unique combination of knowledge and hands-on capability makes LADICIM a strategic partner in tackling the challenges posed by FUTCAN.
“We have a great deal of trust in the Laboratory. They are not only experts in materials, but also have the right equipment. Moreover, they’re capable of rigorously implementing Machine Learning in our scientific work with strong mathematical foundations. Partnering with LADICIM helps reduce the risks associated with this challenge,” says Dr. Alejandro Pérez, R&D&I Project Manager at CTC and coordinator of the initiative.
The Importance of Data
FUTCAN offers LADICIM the opportunity to apply its expertise to optimize industrial processes beyond the metal industry, an area where it has already developed several projects with this objective.
In the case of FUTCAN, the Laboratory contributes its experience and capability to generate real and relevant data using its industrial injection molding machine. The research will focus on the manufacturing of standardized tensile test specimens, with the particularity that each batch will be produced by varying different parameters of the injection molding machine. In a second stage, each produced batch will be physically and mechanically characterized. Thus, during the polyamide injection process, information about manufacturing parameters and resulting properties will be collected.
“An injection molding machine is a highly complex piece of equipment where a large number of parameters can be adjusted and controlled to optimize the injection process and ensure the quality of the produced parts. This makes it an ideal manufacturing process for the project’s purpose, as it enables the generation of a large volume of data and thus facilitates process optimization,” explains Professor Isidro A. Carrascal, Technical Director of LADICIM.
Component manufacturing is the result of a meticulous process involving multiple stages of adjustment and homogenization. Achieving the desired outcome requires an investment of time and materials, which translate into costs. That’s why optimizing the parameters applied to the injection molding machine to produce parts with the desired properties is so important.
“We define the input parameters to feed the model, which we modify on the injection molding machine. On the other hand, the output parameters are defined—describes Professor Carrascal—as the physical and mechanical properties measured on the specimens resulting from the injection process. The research will allow us to obtain a complete data matrix that we will provide to CTC for their future developments.”
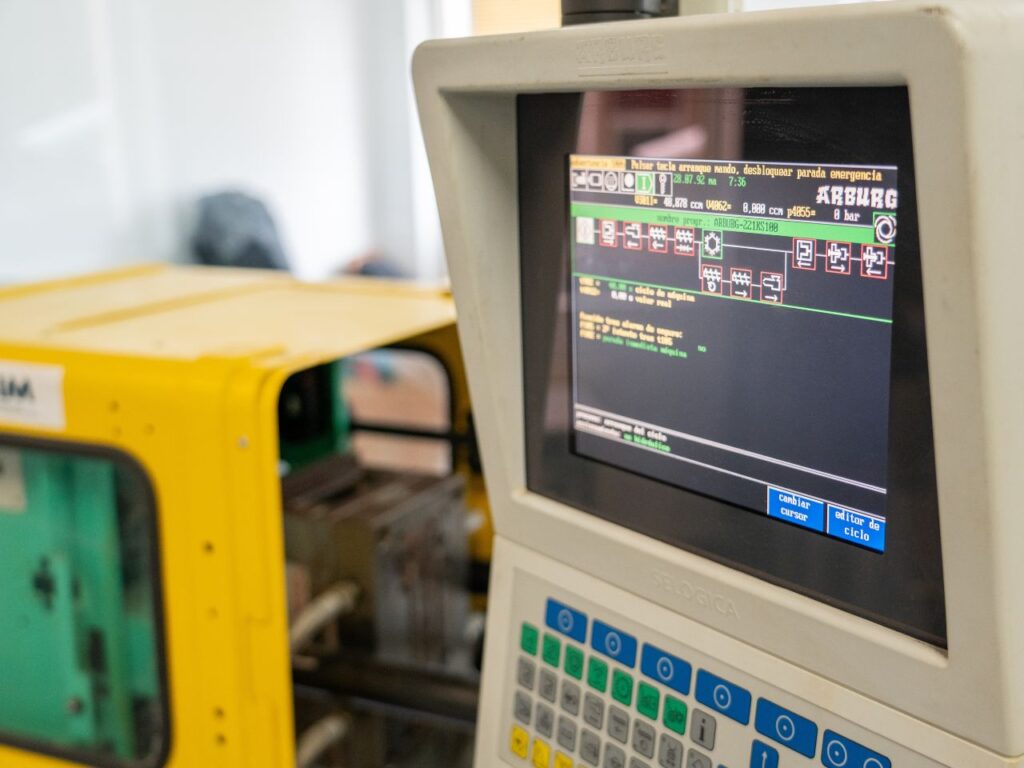
The next step will be up to the researchers at CTC, who, using advanced modeling and data analysis techniques, will be able to identify the optimal manufacturing parameters. “We need to present a feasible challenge and a viable proposal to the Department of Industry, which is why it’s so important that CTC and LADICIM work hand in hand,” says Alejandro Pérez. “The automotive sector is very demanding, and once we achieve the jointly developed functional pilot for the injection molding machine, we’ll be able to enter other sectors more easily thanks to the Laboratory’s extensive knowledge in materials science.”
Efficiency, Sustainability, and Competitiveness
The data generated by the Laboratory will be crucial for training and calibrating the Machine Learning models that CTC will use to optimize the injection molding process. Implementing these advanced technologies will enable precise programming of the machine from the start, saving both time and material in producing the desired component.
Dialogue with potential clients is essential to implement improvements in their industrial processes, but FUTCAN’s work is being carried out confidentially. “We explain the general benefits and they mention that a 20% reduction in material and production time could be achieved, but we believe this rate will increase once intellectual property is secured and the final product is presented,” clarifies Alejandro Pérez.
Reducing time and material contributes to improving efficiency and sustainability and also plays a key role in the competitiveness of the automotive sector, helping to avoid penalties for delays in component delivery. “Major component manufacturers are strict about meeting agreed deadlines, and the market is highly competitive. Therefore, improving manufacturing times is crucial for the sector in Cantabria.”
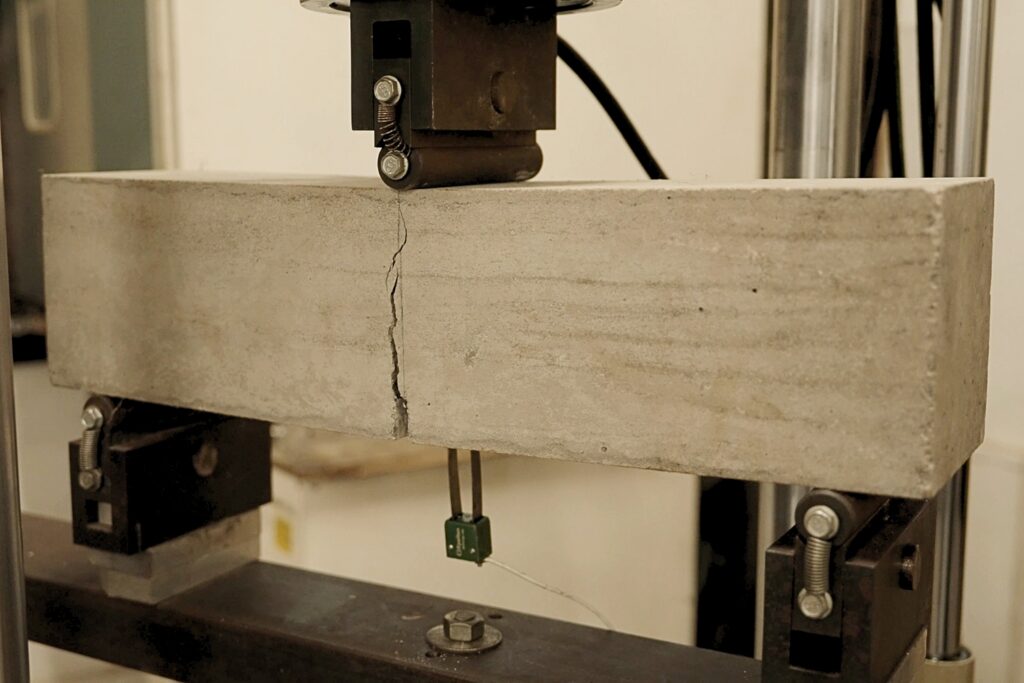
Advantages of Recycled Concrete
Recycled concrete offers a range of technical and environmental advantages that position it as a sustainable alternative to traditional concrete. From a technical perspective, when properly processed and applied, recycled aggregates can provide properties comparable to conventional concrete in terms of strength and durability. This has been supported by research demonstrating its performance as long as established proportions and standards are met.
Environmentally, recycled concrete significantly helps reduce the ecological impact of construction. Its use can decrease the demand for natural aggregates by up to 20%, reducing pressure on natural resources and preventing massive waste generation. Additionally, this material efficiently manages construction and demolition waste, closing the materials’ life cycle.
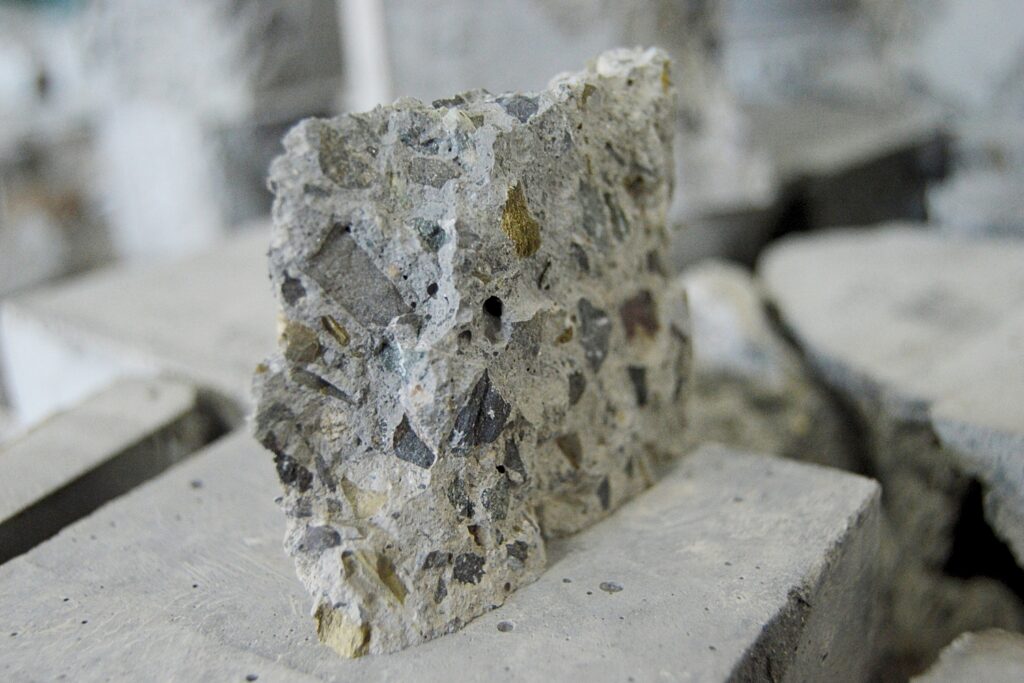
Challenges for Its Implementation
The large-scale adoption of recycled concrete faces challenges that require technical, economic, and regulatory attention. One of the main issues is ensuring the quality and consistency of the material. The inherent variability of recycled aggregates, depending on their origin and processing, makes it difficult to achieve uniform properties, demanding strict control throughout the recycling process—from sorting to treatment. This need increases operational costs and requires significant investment in advanced processing and classification technologies.
From a regulatory standpoint, although frameworks such as Annex N of Eurocode 2 are being developed, the lack of harmonized and standardized regulations at the European level has limited user confidence in the material. This is compounded by insufficient recycling infrastructure. In Spain, for example, less than 15% of construction and demolition waste is recycled, mostly in low-responsibility applications.
This problem worsens in regions where natural aggregates are abundant and cheaper. Lastly, the absence of widespread economic incentives—such as tax benefits or landfill penalties—slows the transition toward using this material. Overcoming these challenges requires a joint effort in technological innovation, effective regulation, and market awareness.
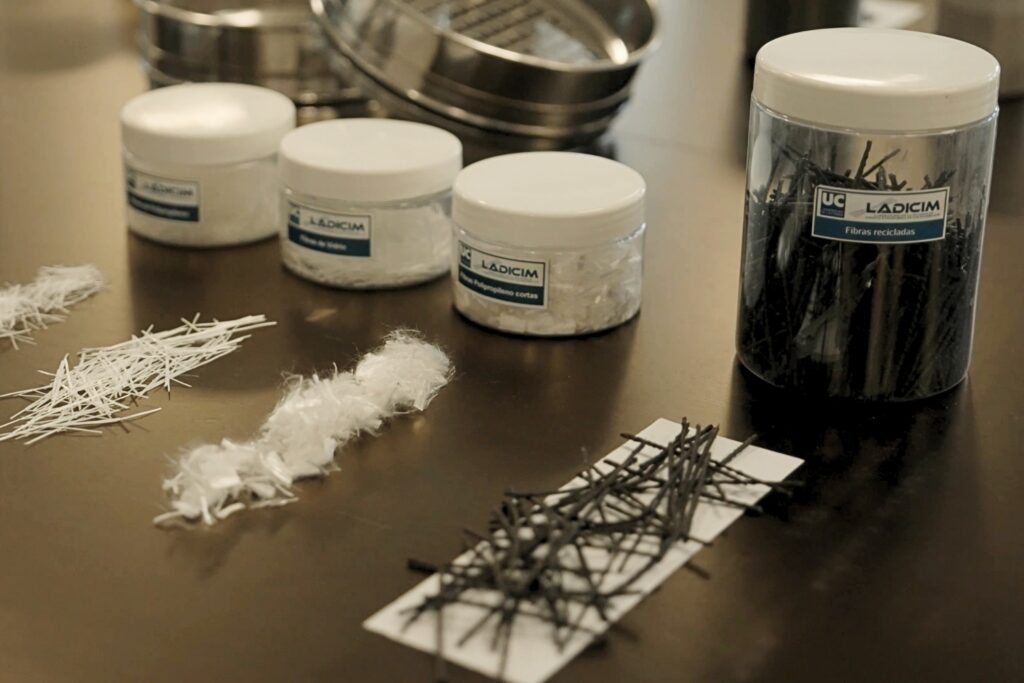
Guarantees for Its Integration into the Construction Industry
To ensure the safety and durability of recycled concrete, strict quality controls are required for recycled aggregates, verifying that they come from structural concrete and are free of impurities such as wood or metals. Regulations like Annex 15 of the EHE-08, and now the Structural Code, limit the proportion of recycled aggregates to 20% in structural applications, ensuring properties equivalent to conventional concrete. Additionally, laboratories such as LADICIM carry out rigorous technical tests to verify compressive strength, durability against freeze-thaw cycles, water permeability, and bonding with reinforcement, guaranteeing performance under demanding conditions.
Recycled concrete must also be adapted to the specific environments where it will be used, such as coastal areas or those exposed to chemical agents, adjusting its composition to meet contextual requirements. Traceability and certification of recycled aggregates, supported by the CE Marking, are essential to ensure compliance with technical standards. Furthermore, innovations such as additives that improve bonding and treatments that reduce porosity enhance the material’s quality and durability, allowing recycled concrete to compete with traditional concrete in terms of safety and performance.