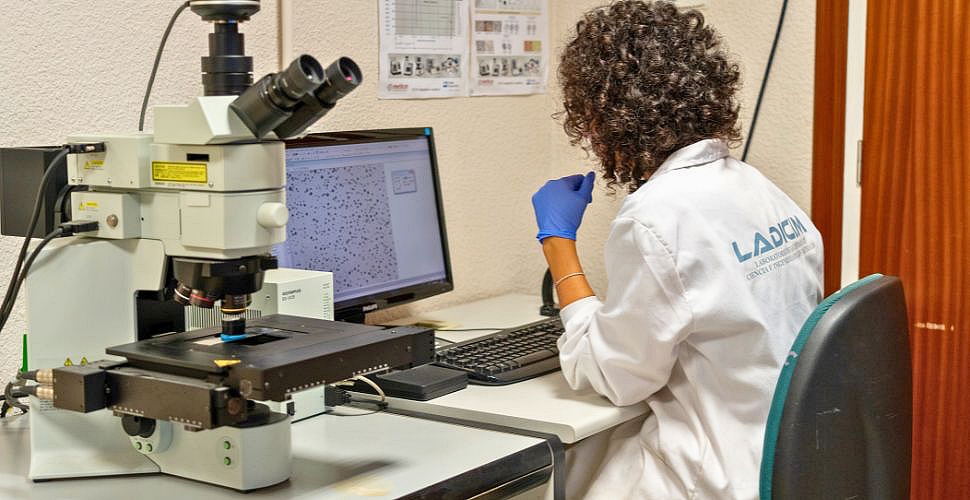
LADICIM and IFCA use AI to automate graphite classification in iron foundries
Using convolutional neural networks, the new system identifies graphite morphology with high precision, overcoming the limitations of manual analysis and enabling more rigorous and efficient quality control.
The proper classification of graphite in iron foundries is essential to ensure that metal parts meet the high quality standards required by strategic sectors such as automotive, industrial machinery, energy, and construction. Graphite, present as particles within the iron matrix, plays a crucial role in the mechanical and thermal properties of the material, directly impacting its performance and durability in demanding applications.
For example, in the automotive industry, ductile iron casting is critical for manufacturing components such as axles, engine blocks, and suspension systems. The spherical shape of the graphite in these applications enhances the material’s strength and ductility, reducing stress concentration points and increasing the ability of parts to withstand mechanical loads and thermal shocks. This extends the lifespan of vehicles and lowers maintenance needs, creating benefits for both manufacturers and end users.
Gray cast iron, on the other hand, is characterized by the presence of flake graphite, making it ideal for components like brake discs and cylinder heads, as it facilitates heat dissipation and vibration damping. This leads to greater energy efficiency and safer, quieter equipment operation, improving industrial productivity and ultimately benefiting the economy.
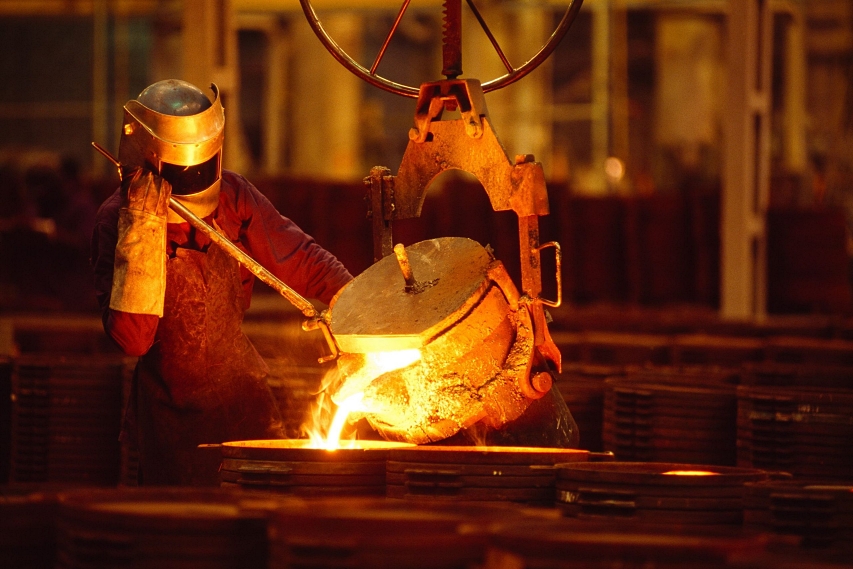
The proper classification of graphite shapes is also essential in construction, where cast components must withstand variable loads and harsh environmental conditions. Vermicular graphite, with characteristics that fall between nodular and flake forms, provides an ideal balance between strength and thermal conductivity, making it optimal for components exposed to constant thermal and mechanical fluctuations.
The ability to accurately identify graphite morphology in foundries not only allows companies to fine-tune their production processes but also ensures the manufacture of reliable and long-lasting products. This has a positive impact on industrial sustainability by reducing resource consumption and waste generation, and it contributes to societal well-being by improving the safety and efficiency of the products we use every day. Thus, the correct classification of graphite is a cornerstone of innovation and competitiveness across various industries, influencing everything from the supply chain to the end user and promoting technological development that enhances quality of life.
Limitations of the Traditional Method for Graphite Classification
Despite its widespread use in the industry, this method presents significant limitations due to its qualitative nature. The classification heavily relies on the operator’s subjective interpretation, which introduces a high degree of variability in the results. Different analysts may reach divergent conclusions when assessing the same microstructure, particularly in cases where graphite shapes transition subtly from one form to another.
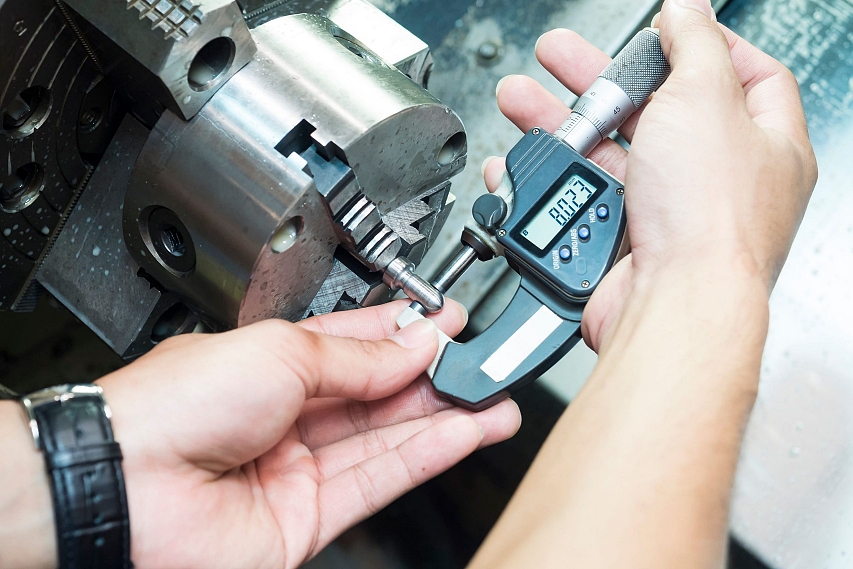
An additional challenge of this system is the evaluation of samples with heterogeneous microstructures, where multiple graphite forms coexist. In such cases, the operator must visually estimate the relative proportion of each graphite type—a complex and error-prone process. The need to manually assess each sample increases the time required for analysis, which in turn raises operational costs and reduces efficiency in high-production-demand environments.
These limitations in the reliability and efficiency of the current system pose a barrier to ensuring consistent material quality—an especially critical issue in applications where the mechanical properties of castings must be precise and stable. In this context, the industry faces the challenge of adopting methods that preserve analytical accuracy while eliminating the biases and constraints of manual processes.
Innovation in Graphite Classification with Artificial Intelligence
In response to these challenges, the Laboratory of Materials Science and Engineering (LADICIM) at the University of Cantabria, in collaboration with the Institute of Physics of Cantabria (IFCA-CSIC), has developed an innovative study on graphite classification in iron foundries, published in the journal Steel Research International. The research team has proposed a methodology that integrates artificial intelligence techniques, thereby overcoming the limitations of traditional visual analysis.
The study, led by Marta Bárcena, Lara Lloret, Diego Ferreño, and Isidro Carrascal, enabled the development of a technique based on Convolutional Neural Networks (CNN) for the automatic classification of graphite microstructures using optical microscopy images. This approach relies on the use of deep neural networks such as MobileNet and U-Net to analyze graphite morphology with precision and consistency, eliminating the subjectivity inherent in manual analysis.
The research is based on a well-known reality: the classification of graphite shapes is essential to determine the mechanical properties of iron castings, yet the traditional visual method suffers from issues of repeatability and accuracy. LADICIM’s work marks a significant step toward automating this process by applying a deep learning approach capable of efficiently analyzing large volumes of visual data.
To address the lack of a sufficiently large dataset for properly training the algorithms, the research team created a synthetic image set based on the reference micrographs provided in the UNE-EN ISO 945-1:2020 standard. This dataset includes 2,400 pure synthetic images (each containing only one type of graphite morphology from the six available families) and 1,500 mixed images (each combining two graphite morphologies), which were used to train and validate the CNN models.
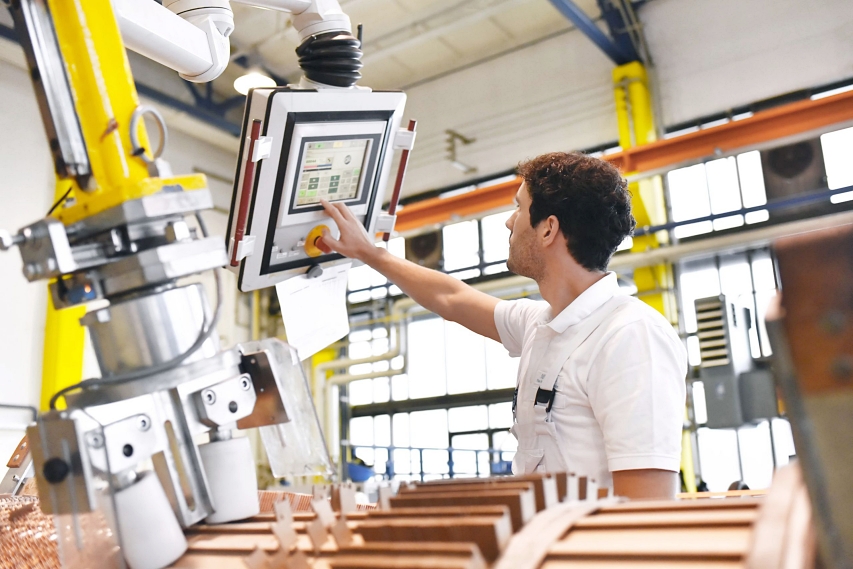
The MobileNet model focused on the classification of homogeneous images, while U-Net was used to segment more complex mixed images, assigning labels to each pixel. This approach allows for detailed identification of graphite shapes in complex samples where multiple morphologies may coexist. The results show that the algorithms can accurately identify the characteristics of graphite, enabling precise classification with an accuracy rate above 97% for pure images, and between 84% and 93% for the segmentation of mixed images.
Moreover, the model demonstrated a remarkable ability to process large volumes of data in a short amount of time—a key feature for industrial applications that demand high efficiency.
An Automated Approach for Real-Time Quality Control
The development of this methodology represents a significant breakthrough, enabling objective and repeatable analysis that ensures the quality of iron castings. The use of machine learning facilitates the scalability of the process and allows for its integration into real-time quality control workflows, improving traceability and optimizing production.
The research carried out by LADICIM and IFCA marks a turning point in the automated classification of graphite in foundries. The collaboration between the two institutions brought together LADICIM’s expertise in materials science and microstructure characterization with IFCA’s experience in advanced data processing and computational modeling. This synergy was key to creating a synthetic dataset that accurately emulated the characteristics of graphite in accordance with ISO 945-1.
Integrating these techniques into quality control processes will enhance the consistency of analyses, optimizing the industrial production of cast components. The proposed automated approach has the potential to be implemented across various industries, improving both the efficiency and quality of production in sectors such as automotive, energy generation, and heavy machinery.